Are Bacteria the Next Big Thing in Fashion?
This article was originally published in December 2023 and has since been updated for inclusion in the Spring 2024 issue of Microcosm.
Bacteria, or rather, bacterial cellulose (BC), a network of carbohydrate molecules excreted by some organisms, can be crafted into everything from handbags to jackets. BC can be generated using organic waste and is biodegradable, making it an attractive solution to an unattractive problem. But how can these bacterial fibers be transformed into fabulous “’fits?” And how soon can people expect to find microbial garments at their favorite clothing store?
The Ugly Side of Fashion
The underbelly of the fashion industry is not glamorous. The process of converting raw materials (e.g., cotton) to products that grace runways and store shelves requires hundreds of thousands of tons of insecticides and pesticides, and millions of tons of fertilizers, oil and chemicals. Textile manufacturing also contributes to climate change, generating ~1.2 billion tons of carbon dioxide every year, or roughly 10% of global greenhouse emissions.
Most pieces of clothing don’t last long in the closets of consumers—in the U.S., the average person throws away an estimated 81 pounds of clothes each year, many after only being worn a few times. When these garments end up in landfills, they can leach chemicals and microplastics into the environment and waterways, which can negatively impact the health of people and the planet.
This picture has propelled a push for practices that “green” up clothing production, including the use of raw materials that bolster sustainability without sacrificing the features that make standard natural and synthetic materials desirable (i.e., comfortability, permeability, flexibility, etc.). It’s a big ask—but bacteria could be up to the task.
The Beauty of Bacterial Cellulose
Bacterial cellulose consists of a meshwork of glucose molecules excreted by various species of gram-negative bacteria. It’s structurally like cellulose from plants that is already used for textile production (think cotton), just with tinier fibers; in its raw form, BC looks and feels a bit like wet leather. Manufacturers grow the bacteria in vats of culture media and harvest the resulting mats of cellulose to make products (the BC is generally washed and treated to remove bacteria and other impurities).
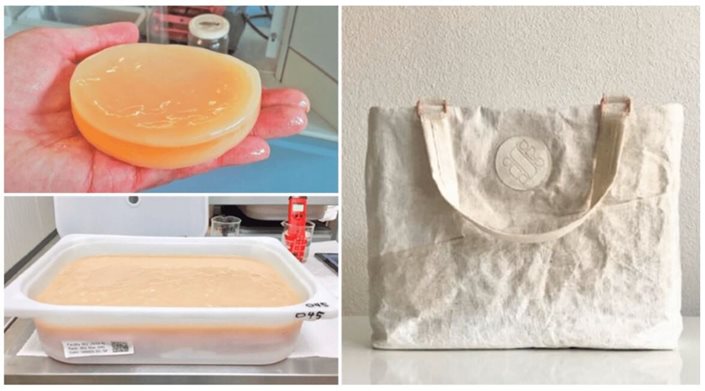
After processing, the final texture is akin to (dry) leather, though it can vary depending on treatment. For example, Modern Synthesis, a U.K. based startup company, grows their bacteria on a framework of thread; the BC fills in the gaps to produce a unique, structured material that looks somewhat like nylon and feels dry and paper-like. Indeed, microbial cellulose is an incredibly flexible material that can be grown to various thicknesses and textures and dyed a slew of different colors. It also has a large surface area, high purity, permeability, dexterity and stellar stability. Moreover, by altering factors like nutrients and oxygen supply—or even the microbes themselves via genetic engineering—producers can modulate BC output and structure.
The Sustainability of Microbial Cellulose
And then there’s the “green” component. BC is a rapidly renewable raw material and can be generated using waste and alternative energy sources. Polybion, a Mexican biomaterials company, uses fruit waste from local producers to feed the bacteria that make BC. This fruity waste would normally end up in landfills and give rise to methane, a potent greenhouse gas. Using the waste prevents the gas from contributing to climate change; it also minimizes the cost required for pricey culture media. Researchers have fed BC-excreting microbes everything from potato peels to wastewater.
There’s also the matter of clothing as a waste product itself. People will throw clothes away—that’s a given. But those made from BC are biodegradable, which shrinks the impact considerably. Malai Eco—a company in Southern India that generates BC using local waste coconut water to produce a leather-like material—notes that their products can be placed in a compost bin, where they will naturally break down. Manufacturing BC clothes using natural dyes (including those made from bacteria themselves) and fewer harmful chemicals than traditional manufacturing processes gives the sustainability factor an “oomph.”
The Future of Fashion
For all its intriguing qualities, BC-based clothing exists largely in the realm of prototype. Polybion debuted a BC jacket developed in partnership with the Danish fashion brand, Ganni, at the 2023 Global Fashion Summit; Modern Synthesis debuted a handbag at the same event. The jacket and handbag weren’t for sale, but simply illustrated the potential of BC. This is common in the BC fashion space—though awareness of microbial cellulose as a raw material has existed for years, products made from the stuff have yet to hit the mainstream market.
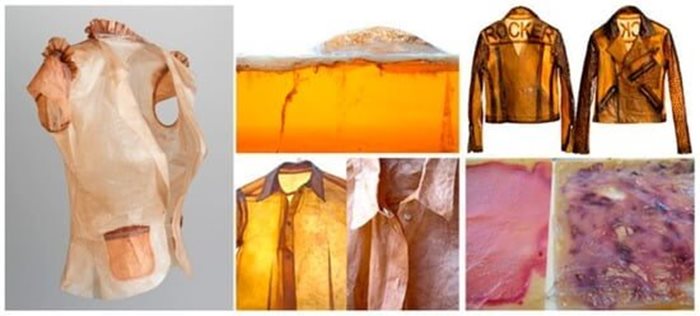
Turning bacterial excretions into wearable clothing requires optimization, which takes time. For instance, BC absorbs loads of water (i.e., is highly hydrophilic), which can be undesirable for making clothes. As such, efforts to confer hydrophobicity to BC while maintaining its flexibility and durability, among other beneficial features, is an important step in development.
Even when a material is ready for consumer use, scaling up production is a lengthy, iterative process that can take upward of 15 years, depending on how ready the technology is and whether the supply chain can support it. This time frame is seemingly discordant with the rapidity with which the fashion industry moves (trends are in, out and in again in the blink of an eye). Because of this, it can feel as though innovations like, say, BC clothes, which generate a lot of buzz during their early development, will never make it to the average consumer.
This isn’t to say it won’t happen, though. Modern Synthesis is exploring how to use existing manufacturing infrastructure to scale up production of their material. Polybion built the world’s first facility for industrial-scale production of BC, and, throughout 2024, is focusing on automating their processes for optimal efficiency. Malai already offers pre-made items and swaths of BC material for purchase.
While the timeline for BC clothing availability may be uncertain, the implications of advancing production are bigger than the potential to snag a cool jacket. The U.S. has made it a priority to bolster the bioeconomy (i.e., the share of economy based on products, services and processes derived from biological resources, like microbes) as climate change looms large. Harnessing the metabolic power of bacteria to literally put clothes on people’s backs is a step in the right direction.
Besides making clothes, bacteria are being used for a variety of applications, including aiding in the detection of disease and environmental contaminants. Check out this next article to learn more.